Aujourd’hui, j’ai adopté des techniques modernes qui simplifient et améliorent le processus. Cela commence par la conception d’un modèle 3D sous Fusion 360.
Une fois modélisé, le fuselage est imprimé en plusieurs sections. Ces pièces sont ensuite alignées et assemblées sur un carré d’aluminium pour garantir un centrage précis, collées à l’époxy, puis finalisées avec un apprêt, poncées et peintes. Enfin, je reviens à une méthode plus classique en utilisant ce master pour créer deux moules en gelcoat et fibre.
Objectif du projet
Pour illustrer ma démarche, j’ai décidé de concevoir un fuselage adapté aux ailes des modèles Pike Perfection et Pike Dynamic, tout en réutilisant leur stabilisateur. L’objectif est de proposer un fuselage polyvalent pouvant s’adapter à différents usages : motorisation, remorquage, vol de pente, GPS ou autres configurations.
L’idée m’est venue en observant le Kazak d’Airtech : un fuselage conçu pour réutiliser d’anciennes ailes de F3J. Ce concept m’inspire à donner une seconde vie à mes ailes de Pike.
Conception sous Fusion 360
La première étape de mon projet est numérique. Grâce à Fusion 360, je modélise le fuselage en partant des dimensions et contraintes imposées par les ailes et le stabilisateur. Ce travail comprend des esquisses précises et une modélisation 3D intégrant des éléments clés tels que les points de fixation, les renforts internes et les tolérances nécessaires pour garantir un assemblage optimal.
Fusion 360 est idéal pour ce type de projet, d’autant qu’il est accessible gratuitement en version hobbyiste. Cet outil puissant offre des fonctionnalités professionnelles, parfaites pour les modélisateurs amateurs comme moi.
Cette étape de conception me permet également de visualiser le fuselage fini et d’anticiper les ajustements nécessaires avant de passer à la fabrication.
Fabrication par impression 3D
Une fois le modèle finalisé, je passe à l’impression 3D à l’échelle 1 (Du moins pour mon modèle de 4m). Le fuselage est divisé en sections adaptées à la taille de mon imprimante (250 mm dans mon cas), ce qui facilite leur production.
Je privilégie des matériaux robustes, comme le PETG, qui offre une bonne résistance mais se ponce difficilement, ou le PLA, plus facile à utiliser mais également plus fragile et sensible aux variations de température.« Après une mésaventure avec du PLA qui a gonflé une fois la peinture faite… je recommande le PETG. »
- Configuration
- Peau extérieure : 3 ou 4 périmètres de 0,4 mm assurent une bonne rigidité.
- Remplissage à 1 % crée une structure légère mais efficace souvent une croix, elle remplie donc sa fonction ou un 15% passe partout qui permet d’assurer une rigidité dans le temps.
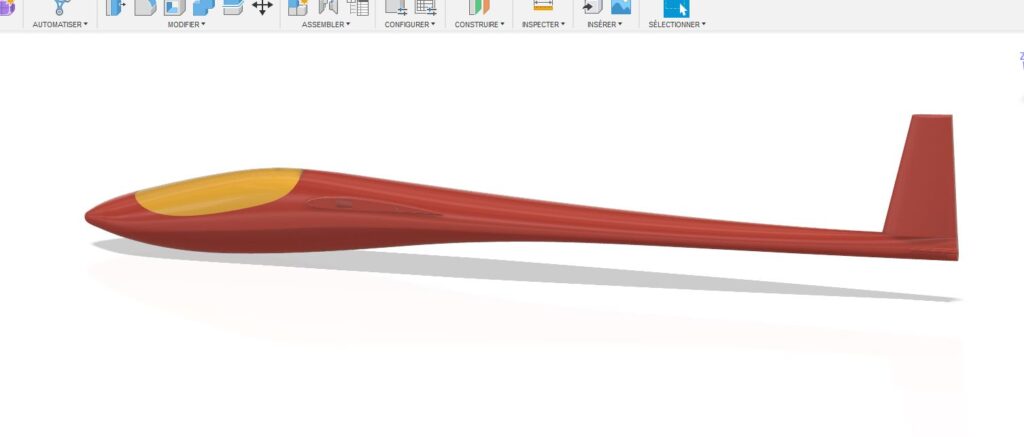
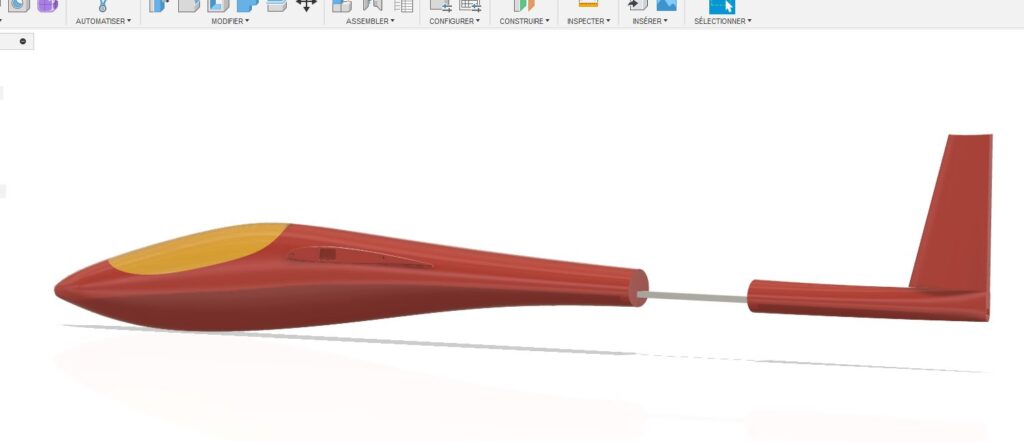
Les sections sont ensuite alignées sur un carré d’aluminium 15×15, qui sert de guide pour un centrage parfait. Cette préparation assure un collage à l’époxy réussi. Une fois les pièces assemblées, j’applique un apprêt, effectue un ponçage soigné et ajoute une couche de peinture PU a 2 composants.
La peinture de chez HP-Textil est une bonne référence et elle vous permettra aussi la peinture dans le moule
Apres création traditionnelle des moules en gelcoat et fibre, à partir du master (pour une 2eme chapitre)